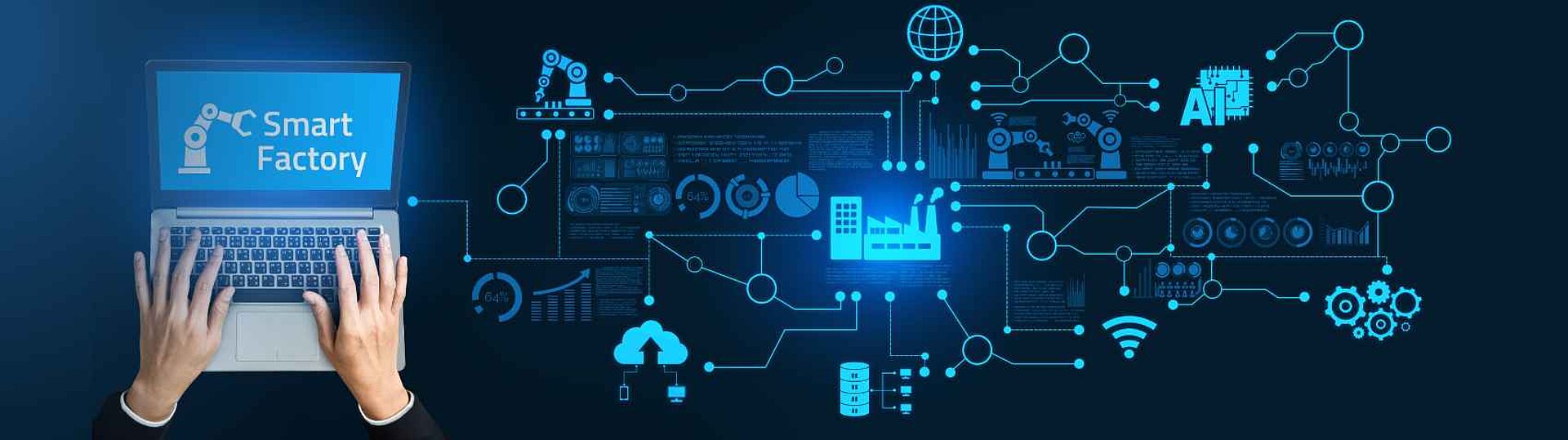
Erfahren Sie, wie Sie mit den Lösungen von MPDV
Ihre Fertigung digitalisieren!
5S Methodology – Smart Factory Glossary
The 5S methodology is a systematic approach with the aim of organizing, optimizing, and standardizing a workspace. The method has its origins in Japan and can be equally applied in the shop floor and office.
Objective of the 5S methodology
The 5S method aims at creating a clean, safe, and efficient work environment. The 5S help organizing the workspace in a way to minimize waste and increase productivity and safety.
The five steps of the 5S methodology
The five S stand for the following steps:
- Sort (Japanese: seiri): The first step involves separating what is necessary from what is not. Everything that is not required is removed to create more space and optimize work environment.
- Set in order (Japanese: seiton): This step is about systematically and logically finding a place for the remaining objects while ensuring easy access. Work is much more efficient if everything has its place and is in place.
- Shine (Japanese: seiso): Regular cleaning and inspecting helps to maintain everything in order and to keep the workspace safe and easy to work in. Problems can be detected at an early stage and the working environment is enhanced.
- Standardize (Japanese: seiketsu): Standards and workflows are developed and implemented to maintain the results of the first three steps. This includes the documentation of processes and training of employees.
- Sustain (Japanese: shitsuke): The discipline among employees to consistently adhere to the established standards is promoted, and the principles of the 5S methodology are integrated into corporate culture in the long term.
Benefits of the 5S methodology
The 5S methodology offers many benefits for manufacturing. By systematically organizing and cleaning their workspace, the employees improve workflows and increase productivity.
- If messy workspaces are eliminated and work equipment is clearly labeled, mistakes can be minimized and workflows streamlined.
- Furthermore, occupational safety is improved as potential risks are promptly detected and eliminated.
- A clean and well-organized workplace makes for a better atmosphere at work and motivates the employees, which in turn enhances the work results.
Altogether, the 5S methodology helps to make optimal use of your resources and achieve continuous improvements in production processes. MPDV's Executive Manufacturing Center (EMC) supports companies in implementing the methodology.
Would you like more information? We are happy to help.
Send us an e-mail. We will take care of your inquiry promptly.