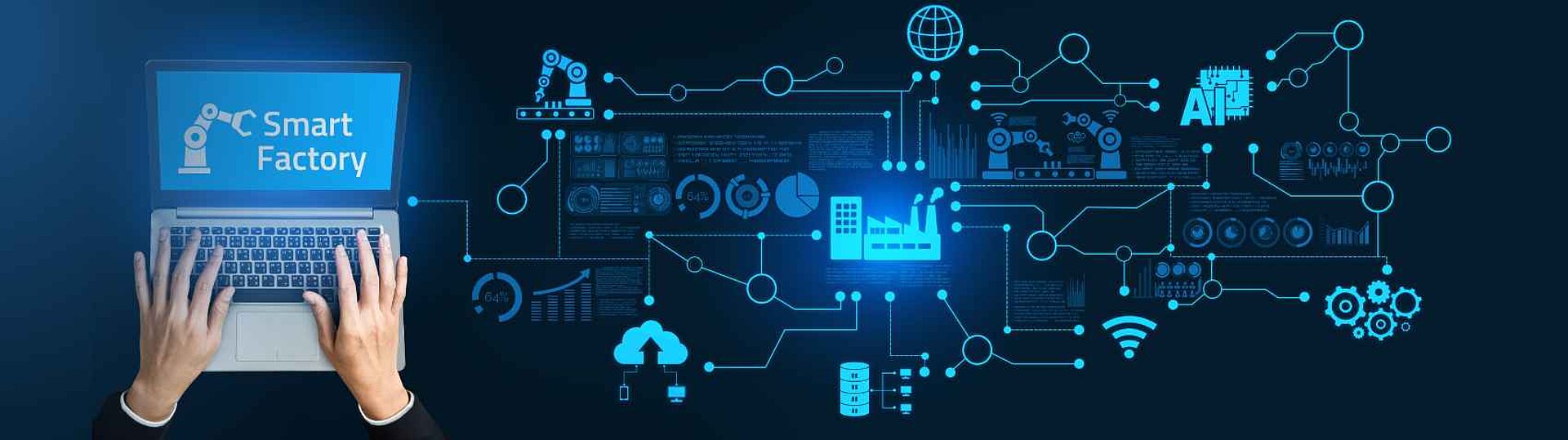
Continuous Improvement Process / CIP – Smart Factory Glossary
The Continuous Improvement Process (CIP) is a lean management method with the aim of optimizing processes, products, or services. The continuous and systematic approach focuses on increasing efficiency and quality while at the same time reducing waste. CIP is one of the key pillars of lean management, which places people at the center of attention. Involving employees, promoting their willingness to embrace change, and encouraging them to rethink their work continually are key elements of the CIP.
The continuous improvement process is never finished. The different steps of the method are constantly repeated. Minor optimizations that are quick to implement take priority over large and lengthy improvement projects. The PDCA cycle, also known as Shewhart or Deming cycle, is a four-step control cycle to implement improvements in line with CIP. After an analysis phase, the PDCA cycle restarts from the beginning. As the name reveals, CIP is a continuous process assuming that improvement is always possible — no matter how good a process or product is.
- Plan: Analyze the as-is state, identify opportunities for improvement, develop concept and project plan, propose hypothesis.
- Do: Develop and adopt optimization measures, test effectiveness, document results.
- Check: Monitor and assess changes. Test hypothesis and implement measures as the new standard if target is achieved.
- Act: Implement newly developed measures as the standard in existing processes and roll out to further areas.
In the plan and check phases, process KPIs play an important role for the success of the CIP. They help analyze the as-is state, identify opportunities for optimization, and check if the implemented measures are effective.
MES supports the Continuous Improvement Process
A Manufacturing Execution System like MPDV's MES HYDRA X supports the continuous improvement process. Based on the data collected by an MES and the ensuing analyses, the overall transparency in production is enhanced. As a result, companies can identify malfunctions at an early stage, react promptly, and minimize the effects. The data from Production Data Collection and Machine Data Collection can be used to perform the first step of the PDCA cycle. Directly at the end of a shift, KPIs such as the Overall Equipment Effectiveness (OEE) including target values are available. If the target is not reached, the responsible people in production can instantly react to improve the current situation. The current KPIs will then reveal if the measures led to the desired result.
- An MES provides information about the most frequent problems in production at the push of a button and supports companies in detecting the relations between malfunctions and their causes. Thanks to the extensive data basis of a Manufacturing Execution System, systematic influences are quickly identified.
- Once the causes are known, people can develop solutions and stop problems.
- Directly after having adopted the measures, their effectiveness can be checked in the MES without having to collect data manually.
- If the optimization measures become the new standard, product-specific information must be changed. Documents such as work instructions or product drawings can be edited in an MES at minimum cost.
A Manufacturing Execution System facilitates and accelerates the continuous improvement process significantly. Thanks to the improved transparency provided by an MES, more opportunities can be uncovered than without an MES.
CIP in manufacturing
The continuous improvement process provides multiple benefits in manufacturing. These include:
- Optimize production processes: The continuous analysis and improvement of production workflows help shorten throughput times, increase productivity, and reduce costs.
- Increase quality: The CIP supports companies in detecting and eliminating failure causes, which will enhance product quality.
- Involve employees: Employees know their way around their own workflows. They can easily give clues on how to simplify things. Involving employees encourages them to identify with the company and motivates them to take an active part in the improvement process.
- Improve resource efficiency: The continuous improvement process helps reduce waste of material, time, or energy. This saves costs and promotes sustainability.
Would you like more information? We are happy to help.
Send us an e-mail. We will take care of your inquiry promptly.